Boeing Hits Back At Whistleblower Claims
17 April, 2024
7 min read
By joining our newsletter, you agree to our Privacy Policy
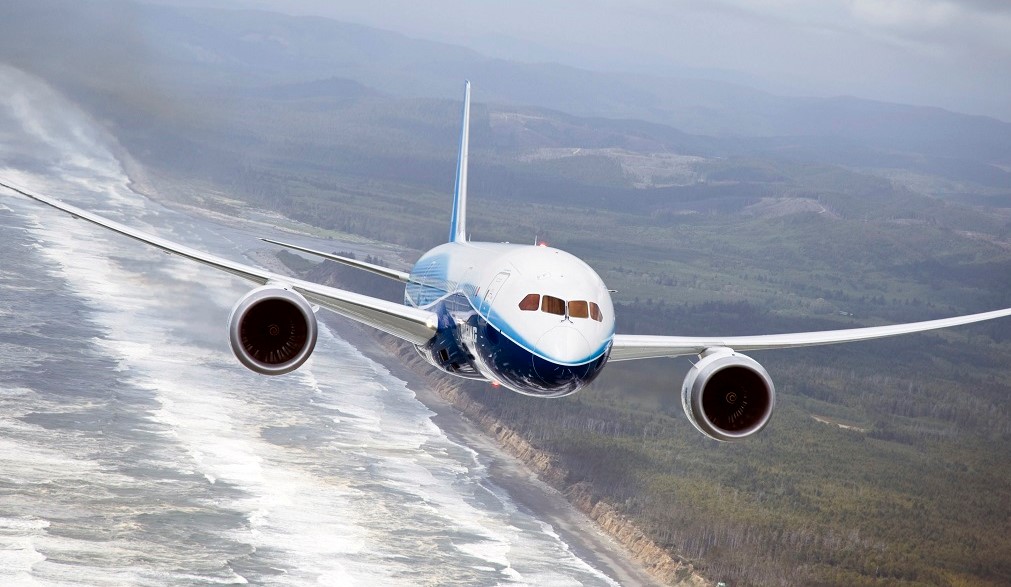
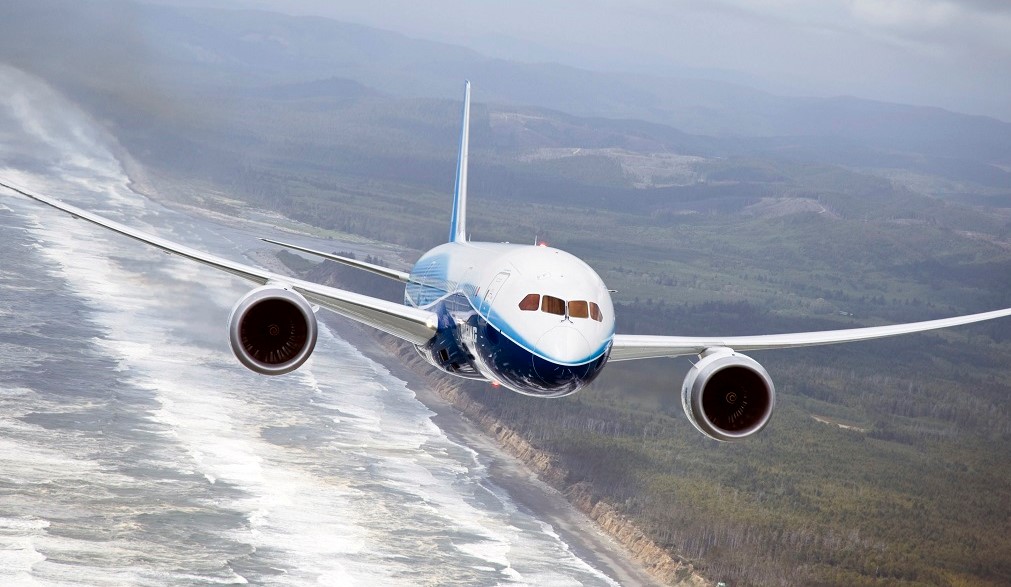
Boeing has hit back at a whistleblower's claims that its 787 and 777 have design weaknesses and are a safety risk'
On April 15 in its North Charleston facility two senior Boeing engineers shared detailed information o the testing and fatigue lives of both the 787 and 777 to the media in a briefing.
Here is a summary of the media call;
Related to the 787 Dreamliner
From Steve Chisholm, Chief Engineer for Boeing Mechanical and Structural Engineering:
- Inspections of the current in-service fleet:
671 aeroplanes have completed 6-year maintenance inspections
8 aeroplanes have completed 12-year maintenance inspections
10 aeroplanes have had intensive structural maintenance evaluations carried out by teams of engineers and specialists.
“Through all of this, there have been zero airframe fatigue findings on the 787 fleet, and all these results have been shared with the FAA,” Mr Chisholm said.
- On minuscule gaps identified in areas where the 787 composite fuselage sections are joined:
“We haven’t identified any safety issues” related to tiny gaps identified in areas where 787 composite fuselage sections are joined together. “We have not seen anything in service related to [the gaps] that would indicate that there is an issue with the in-service fleet.”
Mr Chisholm also added that Boeing is thousands of engineers and mechanics working together on these issues. “This isn't an individual, this isn't a leader, this isn't a specific person deciding this is what we're going to do. Everything's done with the collective, with stress analysts, our tooling engineers, our liaison engineers, our production engineers, our quality personnel, our build personnel and the FAA all involved in these discussions.”
Following Boeing's analysis and FAA review and approval, Boeing has updated certain production methods in the 787 final assembly, including using “fit up force” ranging from 5 to 150 pounds to bring two fuselage sections together before they are joined. Mr Chisholm said this fit-up force is applied to approved areas and is minimal to an airframe designed to withstand thousands of pounds of force.
The company’s full-scale fatigue testing from 2010-2015 of a 787 composite airframe stressed it to the equivalent of 165,000 flights, which was the company’s most extensive testing for any aircraft.
Mr Chisholm said: “There were no findings, zero findings of fatigue in our composite structure, over 165,000 cycles” in those tests.
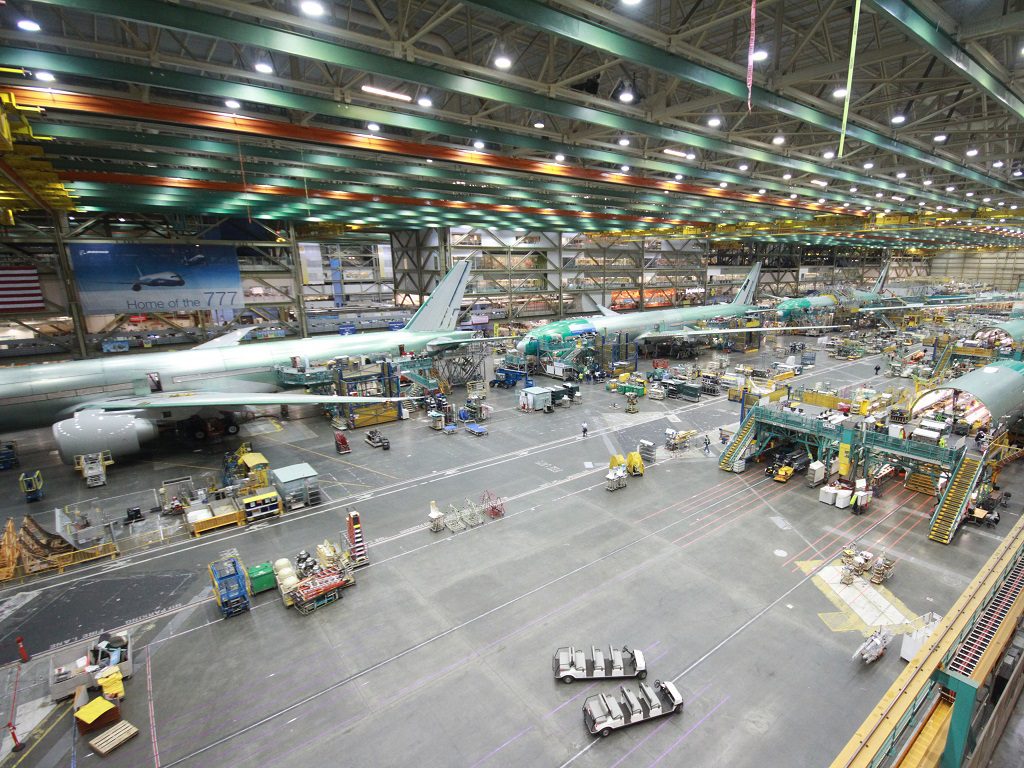
Boeing 777 production line
Because the test airframe was designed and built in the same way as the first 980 aeroplanes in service, Boeing examined the test airframe and data after the more recent issues came to light.
Mr Chisholm: “We were taking out fasteners, we were looking for damage. We're also doing the through-hole inspections to understand the build condition. And we didn't find any fatigue, any fatigue issues in the composite structure.”
Lisa Fahl, Vice President of Engineering, Airplane Programs, Boeing Commercial Airplanes told media “Everything in our design and build system requires substantiation, testing, analysis, and validation prior to implementation on our aircraft and in our production systems. It’s required by our type certificate and our production certificate. Those systems work congruently together to ensure that what we build is approved.”
Ms Fahl added “We’re on a continuous improvement journey to ensure that our teammate's opinions and questions get answered. We hear from them, we create processes, we continue to evolve on this process as we go forward and just welcome the feedback and encourage it and want it from our team, that’s how we make ourselves better, that’s the foundation of the Safety Management System and aerospace safety in general, is people speaking up.”
In 2020 Boeing self-reported issues with the 787 production and halted deliveries to resolve the problems. There were a series of issues and deliveries were halted for almost two years as they were resolved.
On the 787 production, Ms Fahl said that Boeing has collected “well over 1 million data points” by inspecting about 10,000 fasteners on each 787 that join the aeroplane’s composite fuselage sections.
“Every single analysis package data collection process was audited by the FAA and submitted to them for their review and approval. And we went through the comprehensive assessment of root cause corrective action, for every single one of these issues. And then only then when we had gone through all of that did we resume deliveries…And it was, I think, a really proud moment for us because we went tip to tail systemically and looked at our airplane.”
During the 787’s development in the 2000s, Boeing established a conservative standard for a gap between fuselage sections that could only be five-thousands (0.005) of an inch, or about the width of a human hair because the 787 was the industry’s first composite aeroplane.
Ms Fahl said: “What we've learned is that aircraft is highly capable of larger gap allowances, and that's what we went through with the data collection” from 2020 to 2022.
Boeing also launched Boeing 777 production improvements several years ago, including assembling fuselage sections upright and increasing the use of determinant assembly (also known as part indexing) to align parts to tightly controlled tolerances.
Ms Fahl said: “Ultimately, it's really just us looking at our continuous improvement in all of our production systems. We are looking across the board on every program how we make the build more producible, easier for our mechanics to build.”
Mr Chisholm added that airlines have completed 8-year maintenance inspections of more than 1,000 777 jets. Aircraft inspected included 27 777s built starting in late 2015 with the production improvements, and 114 777 Freighters that were built with determinant assembly for the aft fuselage.
Mr Chisholm said: “There have been no fleet findings on any of those inspections” related to newer production methods.
JOIN: AirlineRatings.com YouTube Channel
GET: Accurate MH370 Information From AirlineRatings.com Newsletter
Airlineratings.com is packed with information about air travel and answers questions that many of us may have thought of, but didn’t know who to ask. Well, now you do!
Airlineratings.com was developed to provide everyone in the world with a one-stop shop for everything related to airlines, formed by a team of aviation editors, who have forensically researched nearly every airline in the world.
Our rating system is rated from one to seven stars on safety – with seven being the highest ranking. Within each airline, you will find the country of origin, airline code, booking URL and seat map information. The rating system takes into account a number of different factors related to audits from aviation’s governing bodies, lead associations as well as the airline’s own safety data. Every airline has a safety rating breakdown so you can see exactly how they rate.
Over 230 of the airlines on the site that carry 99 per cent of the world’s passengers have a product rating. Given that low-cost, regional and full-service carriers are so different we have constructed a different rating system for each which can be found within each airline.
Get the latest news and updates straight to your inbox
No spam, no hassle, no fuss, just airline news direct to you.
By joining our newsletter, you agree to our Privacy Policy
Find us on social media
Comments
No comments yet, be the first to write one.