Boeing Blasted in Scathing Report Over Alaska Airlines Door Blowout
17 July, 2025
8 min read
By joining our newsletter, you agree to our Privacy Policy
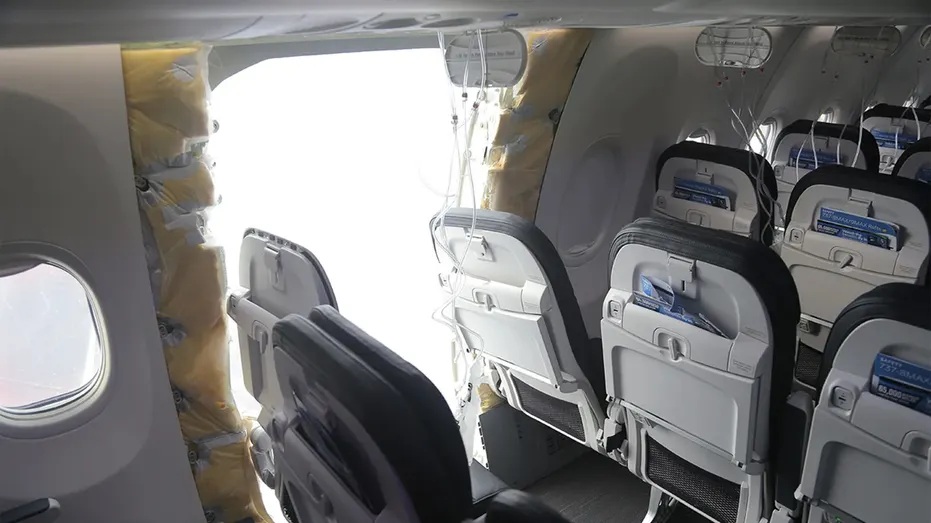
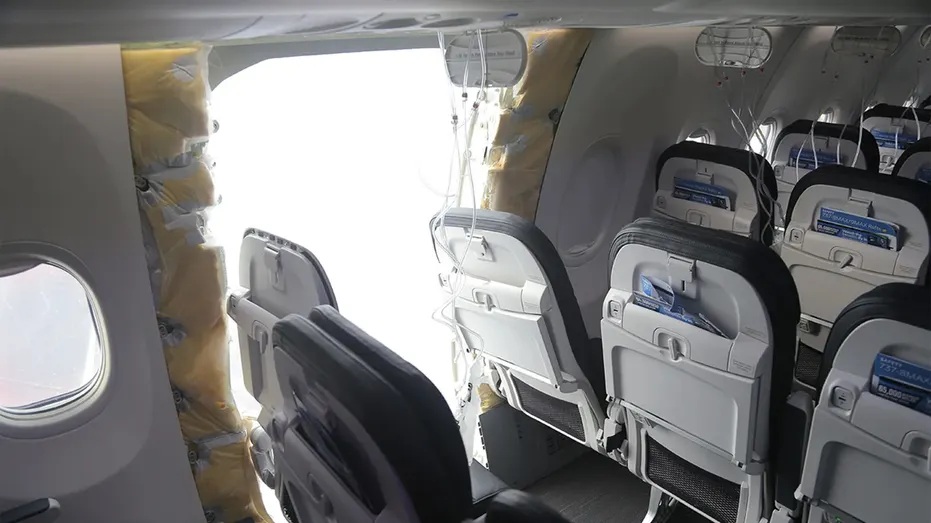
Alaska Airlines Flight 1282, operated by a Boeing 737 MAX 9, departed Portland en route to Ontario on 5 January 2024. At around 16,000 feet, a loud bang was heard, which caused rapid cabin decompression and left a gaping hole in the fuselage. Investigators later identified that one of the cabin windows/emergency exits, its holding panel, and parts of an unoccupied seat (seat row 26) had separated from the aircraft.
The final report into the accident has now been released, and its findings are scathing—placing the blame squarely on Boeing and the FAA.
On 10 July 2025, the NTSB concluded the probable causes of the accident in their final report:
The National Transportation Safety Board determines that the probable cause of this accident was the in-flight separation of the left mid-exit door (MED) plug due to Boeing Commercial Airplanes’ failure to provide adequate training, guidance, and oversight necessary to ensure that manufacturing personnel could consistently and correctly comply with its parts removal process, which was intended to document and ensure that the securing bolts and hardware that were removed from the left MED plug to facilitate rework during the manufacturing process were reinstalled.
Contributing to the accident was the Federal Aviation Administration’s ineffective compliance enforcement surveillance and audit planning activities, which failed to adequately identify and ensure that Boeing addressed the repetitive and systemic nonconformance issues associated with its parts removal process.
During the incident, the flight crew experienced sudden decompression that caused their ears to pop and dislodged their headsets. The captain’s head was pushed into the HUD, and the co-pilot’s headset was torn off entirely. The flight deck door blew open, making communication difficult due to the noise. Both pilots immediately donned oxygen masks, declared an emergency with air traffic control, and were cleared to descend to 10,000 feet. The first officer completed the rapid decompression checklist while the captain flew the aircraft back to Portland, where it landed safely without further incident. Oxygen masks deployed throughout the cabin, and loose items were sucked out. Eight people sustained minor injuries, but all passengers and crew survived.
AirlineRatings CEO Sharon Petersen says, “This had the potential to be an absolute disaster. This accident, in the hands of a highly professional and safety-focused airline like Alaska Airlines, has without doubt prevented another accident or potential catastrophe. This occurrence, in the hands of an airline with sub-par onboard safety practices and less experienced pilots, could have potentially ended in tragedy. This is a perfect example of why Alaska Airlines features in our World's Safest Airlines list time and time again. We absolutely applaud their safety culture and adherence to protocol in the toughest of situations.”
If you’re looking for more detail, the 25 June NTSB executive report outlines the findings (see below), but the key points are:
Four bolts that secured the left MED plug to prevent it from moving vertically were missing before the newly manufactured aircraft was delivered to Alaska Airlines.
Boeing’s Business Process Instruction (BPI) for performing parts removals lacked the clarity, conciseness, and ease of use necessary to be an effective tool for workers in the manufacturing process.
The Federal Aviation Administration’s compliance and enforcement surveillance, audit planning procedures, and records systems were inadequate to identify repetitive and systemic discrepancies and nonconformance issues with the BPI for parts removals.
NTSB executive report
The National Transportation Safety Board found that the four bolts that secured the left MED plug to prevent it from moving upward vertically were missing before the newly manufactured airplane was delivered to Alaska Airlines. As a result, the left MED plug was able to become displaced gradually upward (by fractions of an inch) during previous flights until, during the accident flight, it displaced upward enough to disengage from its stop fittings and separate in flight. The upward displacement before the accident flight would not have been detectable during a routine preflight inspection, and there was no evidence this upward displacement was associated with previous pressurization system AUTO FAIL light illumination events.
We determined that, when the airplane was manufactured, Boeing personnel had opened the left MED plug (which inherently required removing the four bolts and associated hardware) to allow access for rivet rework to be performed on the edge frame forward of the left MED plug. However, opening an MED plug was a nonroutine task, and no personnel experienced with opening or closing an MED plug were on duty at the times that the accident airplane’s left MED plug was opened and closed, and none said they had any knowledge of who opened it.
We found that, per Boeing’s Business Process Instruction (BPI) for performing parts removals, opening an MED plug, because it was a disturbance of a previously accepted installation, required the generation of a removal record. The purpose of a removal record was to document that parts were removed from the airplane and to specify the tasks and quality assurance signoffs required to ensure that the installation was subsequently restored to an accepted condition. However, we found that no removal record was generated. The left MED plug was subsequently closed without its securing bolts and attachment hardware, and no quality assurance inspection of the plug closure was performed. In addition, Boeing’s short stamp process, which was intended to document the work that needed to be deferred or “traveled” to allow for the rivet rework, was not correctly applied for the accident airplane. We found that, although the short stamp process does not negate the need to generate a required removal record for disturbed installations, had the short stamp process been correctly applied, it may have provided an opportunity for personnel to detect the left MED plug’s missing bolts and attachment hardware.
We also found that Boeing’s BPI for performing parts removals lacked the clarity, conciseness, and ease of use necessary to be an effective tool for workers in the manufacturing process. The BPI had a documented history of compliance issues for at least 10 years before the accident. However, Boeing’s corrective actions to address the issues, which were accepted by the Federal Aviation Administration (FAA), were ineffective to address the persistent deficiencies with the BPI.
We also found that Boeing’s on-the-job training for generating removal records was insufficient, which decreased the likelihood that personnel with limited exposure to nonroutine tasks could correctly open an MED plug and generate the required removal record.
We found that the Federal Aviation Administration’s (FAA) compliance and enforcement surveillance, audit planning procedures, and records systems were inadequate to identify repetitive and systemic discrepancies and nonconformance issues with the BPI for parts removals. Also, Boeing’s quality escape guidance did not adequately address controls for human error, and its voluntary safety management system, which was still being developed at the time the accident airplane was in production, did not proactively identify the risk of the quality escape that occurred. We determined that, for Boeing’s future implementation of its regulatory safety management system (SMS) and integration into its quality management system to be successful, accurate and ongoing data about its safety culture is needed.
We also found that the circumstances of this accident and others in which the flight crew faced communications challenges associated with oxygen mask use highlighted the need for hands-on, aircraft-specific training and procedures for the use of each type of oxygen system in an operator’s fleet. We also identified the need for the FAA to review the design standards for portable oxygen bottles to ensure that they adequately address ease of use.
Further, the circumstances of this accident emphasized the need for effective operator procedures for preserving cockpit voice recorder (CVR) data after an accident or incident occurs, as well as the continued need for installations and retrofits of CVRs with a 25-hour recording capability. We found it continues to be necessary to address these issues because valuable information continues to be overwritten on CVRs that are designed to record only 2 hours of audio data. Finally, although the three lap-held children on board the accident airplane did not sustain any injuries, we found that the potential for severe injury or death existed and reinforced the prudence of using a child restraint system (CRS) for children less than 2 years old appropriate to their size and weight.
The flight crew said their ears popped, and the captain said his head was pushed into the heads-up display (HUD) and his headset was pushed up, nearly falling off his head. The FO said her headset was completely removed due to the rapid outflow of air from the flight deck. Both flight crew said they immediately donned their oxygen masks. They added that the flight deck door was blown open and that it was very noisy and difficult to communicate.
The flight crew immediately contacted air traffic control (ATC), declared an emergency, and requested a lower altitude. The flight was assigned 10,000 ft. The captain said he then requested the rapid decompression checklist, and the FO executed the required checklist from the Quick Reference Handbook (QRH). As the FO completed the checklist, the captain flew the airplane as they coordinated with ATC to return to the PDX airport. The flight landed on runway 28L without further incident and taxied to the gate.Oxygen masks deployed, loose items (phones, headset, clothing) were violently pulled out, and the flight crew initiated an emergency descent and returned safely. Eight people — seven passengers and one flight attendant — sustained minor injuries; everyone survived.
Get the latest news and updates straight to your inbox
No spam, no hassle, no fuss, just airline news direct to you.
By joining our newsletter, you agree to our Privacy Policy
Find us on social media
Comments
No comments yet, be the first to write one.